EBERBACH, Germany — May 5, 2021, 2021 — As a machine manufacturer DiloSystems provides production lines for any nonwoven process and all types of staple fibre products. Looking back on a difficult year 2020, positive developments and a recovery in many industry sectors are now underway. DiloGroup with DiloSpinnbau, DiloTemafa, DiloMachines and DiloSystems as the general contractor delivers the complete range of machinery needed to produce needled nonwovens, and together with partners, thermobonded and hydroentangled nonwovens. All over the world, Dilo lines produce nonwovens for a wide range of applications including geotextiles, housing and roofing, automotive products, filtration, acoustics, artificial leather and medical or hygiene products.
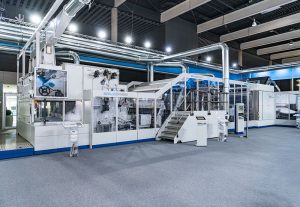
DiloGroup lines can be supplied turnkey from the general contractor DiloSystems as your partner for a coordinated, professionally managed investment with a single responsibility to fulfil all needs technically and commercially. The complete staple fibre process equipment, starting at fibre preparation (DiloTemafa), continuing with webforming by carding (DiloSpinnbau), up to crosslapping and needling (DiloMachines) is built in-house by Dilo’s highly specialized departments. These complete line projects are developed in close contact with our customers and on the basis of textile technological research and studies carried out in our technical centre in Eberbach, Germany.
Recently Dilo added water entanglement lines to its portfolio by cooperating with SICAM S.r.l., a well-known producer of high- quality machinery for the nonwovens industry. Apart from state of the art spunlace lines, DiloGroup is able to fulfill demands and requirements for products having improved tensile strength ratios with Dilo high-speed carding and layering technology.
In 119 years of history, the company has always set new standards regarding machine performance and efficiency. Innovative technologies like DI-LOUR, DI-LOOP and Hyperpunch-needling have created new markets for the nonwovens industry and pushed needlepunch technology to be one of the most important and versatile entanglement processes. New approaches promise higher productivity, quality and ground breaking possibilities for nonwoven textiles.
“diloline 4.0” smart manufacturing is available to be used on every line. Numerous information modules can be recalled via mobile apps and cloud data (mindSpheres). These methods allow the user to improve control of the machines and to generate production data to further secure the complex functions within the production system independently of personnel and shift. Standstill times are decreased.
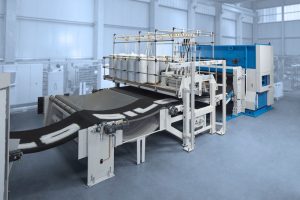
The 3D-Lofter technology is adding numerous possibilities to nonwovens. It works like a 3D- printer whose ink consist of fibres and the addition of adjustable amounts of fibre in a specific pattern on top of fibre mats or needled felts enables applications like decorative features, precise reinforcement or improved fibre mat quality. Furthermore, nearly all fibres like PES, carbon or natural fibres are usable.
Also in the classical needling process Dilo achieves steady improvements. The recently developed needle pattern 8000X generates a new level of homogenous surface based on even distribution of stitches. At the same time, this needleboard allows a high stitching density at high line speeds, due to the high number of needles. Furthermore, related patterns like 6000X are ready to be used in Hyperpunch needlelooms.
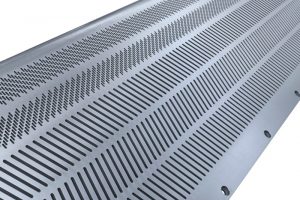
“Microneedling” has been developed as an alternative to water entanglement. Optimized kinematics and maxed out stitch density generate intense but gentle needling at a high line speed. These fabrics can match water jet products regarding quality and productivity at a weight of 60 g/m2 and more. The main advantage here is the low energy consumption, since no high pressure and water processing is needed, which will gain importance in upcoming challenges to the industry for a low CO2 footprint.
These and other fibre processing and nonwoven fabric related topics can be discussed in detail with DiloGroup during ITMA Asia from June, 12 to 16 , 2021 at our booth No. A09 in hall H7.
Posted May 5, 2021
Source: DiloGroup