PARIS — November 16, 2023 — The adoption of composite parts based on flax fibres by the Marine Industry continues to grow, with major OEMs as well as smaller shipyards now aiming to take advantage of the reduced carbon impact and impressive mechanical properties they can provide.
“Over the last ten or fifteen years, several innovative flax fibre boats have been built and the fibre has started to gain significant traction,” says Julie Pariset, Innovation & CSR Director at the Alliance for European Flax-Linen and Hemp. “In addition to the environmental benefits, manufacturers are realising significant technical and processing gains with flax fibre composites.”
“Flax is a very low-density fibre, with a high specific stiffness,” she explains. “It can be used to manufacture composite laminates with mechanical properties not dissimilar to typical E-glass composites and the coefficient of thermal expansion of a flax fibre epoxy part is also quite close to that of a carbon fibre part.”
This allows the materials to work well in combined assemblies with carbon fibre composites and the flax parts are also highly impact resistant.
Flax fibres also provide impressive acoustic and vibration damping in composite applications, as well as providing a warm and aesthetically pleasing appearance below decks.
“Flax yacht interiors can create a more pleasant environment for passengers with less noise and harshness than standard composites,” says Pariset.
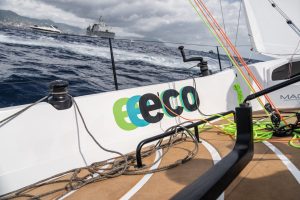
ecoRacer30
As a member of the Alliance for European Flax-Linen and Hemp, Bcomp, headquartered in Fribourg, Switzerland, has this year been working with Northern Light Composites (nlcomp), based in Monfalcone, northern Italy, on the creation of what is billed as the first fully recyclable nine-metre-long sailing boat – the ecoRacer30.
The boat is based on nlcomp’s proprietary rComposite technology – a combination of thermoplastic resins and BComp’s ampliTex high-performance natural fibre reinforcement fabrics and patented powerRibs technology.
It was built in a collaborative effort with the help of Barcelona-based Magnani Yachts, which took care of the composite manufacturing, and Sangiorgio Marine, which provided technical assistance as the boat was being assembled at its shipyard in Genova, Italy.
Magnani Yachts has subsequently become the first shipyard to hold an rComposite license and others are now being encouraged to adopt the technology.
“As the most commonly used material in boat building, fibreglass is not easily recyclable,” says Fabio Bignolini, CEO of nlcomp. “Consequently, many fibreglass boats end up being burned, sunk or abandoned. In the European Union, there are an estimated 80,000 abandoned boats with only one in twenty disposed of in an environmentally responsible manner.”
The second ecoracer30 is currently under construction and has already been sold and nlcomp is planning to build a fleet of eight of these boats in time to enter a series of regattas in the summer of 2025.
Flax 27 Daysailer
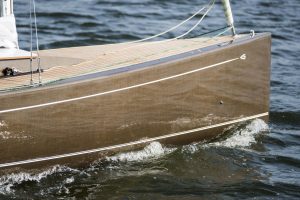
Greenboats, based in Bremen, Germany, is another specialist in building boats from natural fibre composites and has this year launched the Flax 27 daysailer.
The lower hull of this vessel is also made from Bcomp’s ampliTex technical fabrics in combination with a sandwich core of recycled PET bottles. Using a vacuum infusion process, the fibres were integrated with a plant-based epoxy resin in order to further reduce the CO2 footprint of the vessel.
The light structure and modern shapes of the lower hull of the boat result in very fast, sharp and agile handling on the water.
Greenboats has also recently announced significant new backing from alliance member Groupe Depestele, which manages 13,000 hectares of flax land in Normandy, France.
“We’re at a pivotal juncture in the evolution of natural fibre composites as a new product category,” says Jan Paul Schirmer, managing director of Greenboats. “Our clients believe in our technology but demand a more reliable and scalable supply chain. Our partnership with Groupe Depestele will go a good way to establishing this.”
Expectations
Different expectations for the performance of parts must be guaranteed, such as impact resistance, rigidity, surface appearance and resistance to hydrolysis, which is simpler with an established supply chain.
The Beneteau Group, based in Croix de Vie, France, for example, manufactures more than 30,000 composite parts per year to equip its boat decks and is looking to incorporate more natural fibres into them.
This year Beneteau Group has collaborated with Chomarat on the development of hybrid composites of glassfibre and hemp. The resulting Ter2a Mat was a finalist in this year’s JEC Innovation Awards.
Blue Nomad
A project in Switzerland has meanwhile proposed the use of flax fibre composites in solar-powered habitats designed for comfortable living on the oceans – as the world grapples with the frightening implications of climate change and rising sea levels.
As envisaged by students from Institut auf dem Rosenberg in St Gallen, Switzerland working with Denmark-based SAGA Space Architects, Blue Nomad structures would form modular blocks to establish large communities and oceanic farms.
It’s a striking vision of a future where the lines between land and water blur, and sustainability and community building lie at the heart of new human settlements.
The vision is not just theoretical however – plans are now being made for a maiden voyage of a Blue Nomad home across Europe to promote ocean sustainability and climatology.
The project’s scale models for the London exhibition, as well as the first Blue Nomad structure, are based on natural fibre composites again employing BComp’s ampliTex flax fibres in gradient designs, along with a natural bio-resin.
Monitoring the marine market as pioneers in new composite development, Alliance for European Flax-Linen and Hemp continues to be amazed at the innovation and pace of development. Whatever the future holds, it appears flax fibres and natural fibre composites will have an important role to play.
Posted: November 16, 2023
Source: The Alliance for European Flax-Linen and Hemp