Quality monitoring by trial and error is outdated, as is quality assurance and control from the laboratory. Modern and efficient lab equipment is linked online with the production process. A tool from Loepfe Brothers Ltd., Switzerland, counts the yarn imperfections and monitors and evaluates the yarn surface at the same time.
Continuous monitoring and optimization of the production process are decisive factors for consistent yarn quality. Complete quality monitoring provides information on raw material and machine parameters. It also enables reliable detection, and separation when necessary, of off-standard bobbins during winding.
Staple fiber yarns often have imperfections such as frequent smaller yarn faults or irregularities, which are related either to the type of raw material or to an inferior manufacturing process. Isolated faults of this type do not disturb the yarn as such, but too many faults can negatively affect fabric appearance.
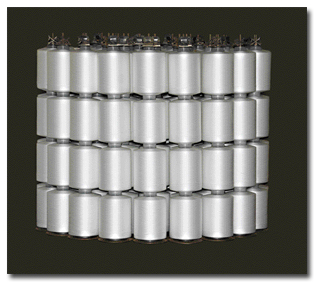
Higher yarn hairiness is often apparent after dyeing, when warp and weft yarns show different absorption capacities.
Types Of Imperfections
Types of imperfections include thin places, thick places and neps.
Together with impairment of the appearance of the fabric surface, the number of thin and thick places is important information concerning the condition of the raw material and the manufacturing process. An increase in the number of thin places does not necessarily mean that the number of machine stops increases during weaving and knitting. Often, thin places indicate larger yarn twists.
With thick places, the higher fiber count in the yarn cross section results in higher torsion resistance. Thick places, therefore, often have less yarn twist. In weaving and knitting, they can be weak points that lead to machine stops. These considerations apply particularly for ring-spun yarns.
Apart from their strong influence on the appearance of the fabric surface, neps from a certain size lead to problems in knitting. Both the size and the number of neps are decisive criteria as to a yarn’s usability.
Neps in the raw material are mainly foreign matter such as shell or plant residues, whereas neps in production are created during spinning through unsuitable machine settings and a bad ambient climate. Most raw material neps are separated during combing. Neps in the finished yarn derive mainly from the manufacturing process. Reliable analysis of imperfections (IPI) allows optimizing manufacturing processes and can also determine fiber material quality.
Yarn irregularity identifies general diameter variations in the yarn. Yarn uniformity is the most important criterion for smooth production processes with regard to characteristics such as thick places or fiber fly as well as differences in yarn count, tensile strength, elongation and twist. Increased yarn irregularities negatively influence quality, leading to more machine stops in downstream processing and to inferior results for woven or knitted fabrics.
Counting Imperfections
Tests show that online counting of imperfections and irregularities of a ring yarn during winding provides important data about yarn quality. Loepfe’s LabPack online quality assurance system reports the number of imperfections per 1,000 meters as well as the small irregularities per meter in the yarn. The system’s online monitoring of the yarn surface to determine the surface index (SFI) enables making a 100-percent quality statement as to the surface characteristics of the yarn to be wound. Only a combination of various quality criteria such as hairiness or irregularity allows a reliable statement. The quality characteristics merge within the SFI, allowing users to monitor quality changes in surface characteristics online.
Hairiness
In order to be able to forecast yarn behavior in the weaving or knitting mill, single quality characteristics such as yarn irregularity are not sufficient. Higher yarn hairiness is often apparent after dyeing, when warp and weft yarns show different absorption capacities.
Hairiness is defined by the number of fiber loops and ends sticking out of a yarn. For spun yarns, it is a parameter that mainly depends on the characteristics of the raw material, spinning mill preparation and spinning process. Contributing factors include: wide spinning triangle; high distortion; friction on deflection points; unsuitable coverings/aprons; dry rooms; or static electricity.
Certain hairiness can be produced as required in downstream processing depending on the application, and can provide a certain effect on the fabric, such as a soft touch. On the other hand, higher or variable hairiness can cause an undesired cloudy appearance, particularly for knitted fabrics after dyeing and finishing.
Higher hairiness in warp yarns can also complicate weft insertion, especially on air-jet weaving machines. Hairy warp yarns can stick together and hinder weft yarns from passing through the weaving shed.
Yarn Count And Clearing
The user defines the constant off-standard bobbin detection (SFI/D) reference value, which remains the same during the entire production and is not adapted automatically by the clearer. Stable production conditions such as climatic conditions must be presumed when using this setting.
During yarn clearing, SFI/D allows reliable detection of quality changes with regard to yarn surface characteristics. If the values are above or below limits set as percentages relative to the SFI/D reference value, off-standard bobbins are detected and removed from production.
The reference value serves as a starting point for SFI/D monitoring. This is either determined continuously by the clearer or entered by the user.
The floating SFI/D reference value adapts to the general yarn surface level of a style. This compensates surface fluctuations caused by climatic conditions and does not lead to excessive cutting counts. Single bobbins with high deviations from the mean value are detected reliably.
The higher the yarn count, the lower the yarn’s breaking strength. Increasing yarn twist provides the required tensile strength. Tests have shown that the SFI sinks as yarn fineness increases. The relation of the sum signal, which reflects the fiber ends projecting out of the yarn, increases as the yarn diameter decreases.
Yarn clearing is vital to meet the increasing demands on yarns. Extensive tests by yarn manufacturers combined with direct cooperation with the customer determine the clearing limits for the respective yarn.
The SFI within a bobbin is spread up to ±10 percent, mainly due to tension differences during ring spinning. Yarn tensile strength fluctuates during bobbin winding and the ring rail stroke. Tensile strength peaks are very large in the area of the bobbin base. Increasing tension leads to deterioration in yarn irregularity and IPI values. These relations must be considered when setting the limit values because such fluctuations do not normally negatively influence quality in the textile surface structure.
Online quality monitoring can be combined with a central data collection system such as the Loepfe MillMaster®, which allows data storage and chronological quality tracking based on graphical representation over a longer period.
April/May/June 2014