New technologies are positioned to become potential market leaders in the increasingly sophisticated world of textiles.
By Edward C. Gregor
The history of textiles began in unrecorded history, when animal skin and vegetation were likely the only available materials according to anthropologists. Fast forward to today, and the world of textiles is well-established, generally sophisticated with a large variety of fibers and constructions routinely sold, and expanding globally in recent years. A view from a high-level perspective finds both commodity and specialty materials — produced as woven, knitted and nonwoven fabrics in forms from natural, synthetic, inorganic, including bio-polymer materials — now emerging. Tweaks in construction by some are considered and promoted as advancements in the state-of-the-art. Other times, wholesale new ideas — some revolutionary, others evolutionary — from thinkers, entrepreneurs and others in R&D and product development, create new entrants. In time, a few of the better tweaks and innovative new technologies will penetrate existing markets and applications displacing incumbent materials. This article highlights several advances, and attempts to sort through the clutter and identify a few technologies positioned to become potential market leaders.
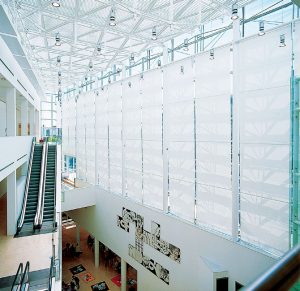
Non-Toxic FR Alternative To PVC
Fire resistance (FR) and intumescent materials are a “hot” topic and receive lots of visibility in many markets including protective apparel, mattresses and contract fabrics — areas where the public gathers indoors.
Atlanta-based specialty plastic compounder Dynamic Modifiers LLC has developed highly-sustainable, lightweight and non-toxic FR compounds and concentrates able to pass NFPA-701 and Cal 19 testing. When used to produce fibers, yarns, films or sheets, PAL…the Clean Plastic does not carry a flame and produces minimal quantities of smoke, therefore creating time to escape from a closed environment. The material can be extruded, calendered or molded into virtually any configuration. “With PAL…The Clean Plastic product line of custom formulated compounds, we believe we offer customers a versatile range of properties and performance often associated with flexible PVC [polyvinyl chloride],” said Howard Bradshaw, president, Dynamic Modifiers.
The company also offers light-weight intumescent low-toxicity compounds and concentrates, but these products require a sheet thicknesses of at least 0.020 inches to be effective. However, the company is working toward versions that will be effective when turned into a thinner sheet.
Wicking And Stain Resistance
Founded in 1993, Bloomfield Hills, Mich.-based Crypton LLC is widely known for its stain-resistant upholstery and the Nanotex® technology. In expanding the company’s reach, Crypton has upped the stakes with a new performance technology called Wick+Block® for apparel. This fabric enhancement is a relatively new offering and an example of a company extending its fundamental technology into new markets to broaden its core competency. Wick+Block is a wicking and stain-blocking treatment for nylon or polyester apparel that rapidly moves moisture away from the wearer, while also adding perfluorooctanoic acid (PFOA)-free stain-resistant properties to a garment. Early uses have included National Football League and college football uniforms that provide players with a fresh clean garment after each and every laundering. A second line extension from Crypton is Nanotex® DRY INSIDE technology for cotton, the result of collaboration with Cary, N.C.-based Cotton Incorporated. Dry Inside is designed as a moisture-management system that rapidly pulls moisture away from an athlete’s body to the outside atmosphere with high-efficiency. “The marketplace for apparel companies is as competitive as ever, so each player is looking for the next technology that will provide an edge,” said Hardy Sullivan, vice president, Market Development. “We want Nanotex to be the go-to innovator for product differentiation.”
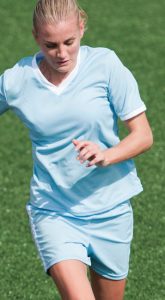
Ceramic Nonwoven
A unique ceramic fiber product is offered by CerX Filters LLC, Johnson City, Tenn. Traditional ceramic filters are tubular in shape and produced from sintered ceramic powders. They are costly and heavy featuring poor flow rates because of minimal porosity for liquid or air flow.
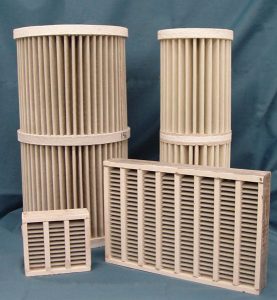
CerX has changed the paradigm, using robust pleated ceramic fiber filtration media with much lighter weight, lower-cost, higher surface area and flow rates, and higher porosity than traditional ceramic filters. These filters operate at temperatures of up to 1,000°C at any pH during extreme conditions. “Low backpressure/high temperature opens many new opportunities for filtration applications,” said Dick Nixdorf, chief technology officer, CerX.
Potential applications reduce particles in diesel engine exhaust and biomass syngas, as well as pre-filtering for catalytic oxidizers. The filters can trap particles, such as lint or carbon fibers, then safely be taken to a high-temperature periodically using a dual-chamber system to cleanse itself in-situ for nearly continuous 24-hour operation.
Performance Knit Fabrics
Malibu, Calif.-based Fabdesigns Inc. is a developer of prototype knit fabrics for use in performance applications. Many of the world’s leading companies seeking to set themselves apart from competition contract to develop new products with Fabdesigns. Because of confidentialities with clients, release of company names, products and insights are restricted.
However, Fabdesigns was permitted to mention one recent non-confidential development, namely a fully-integrated knitted net pocket used in Warrior®-brand lacrosse stick baskets. The 3-D knitted nets are said to provide an accurate feel and control in the throat, pocket and head. The product features a longer channel for reduced friction and a more precise release with a design branded Warp. Examples of other well-known specialty products in Fabdesigns’ past have included one-piece athletic shoes, military applications, medical products, aerospace parts and personal protection garments.
Let There Be Light!
France-based Saint-Gobain S.A. has been making its SHEERFILL® architectural membranes for more than 40 years. Over these four decades, it has developed and introduced new products to meet the changing needs of the structural membrane market. These innovations include membranes in different weights and strengths to better suit the demands of various structures; acoustical membranes for interior applications to reduce noise and reverberation; mesh materials for breathable façades; and even true self-cleaning action with the advent of EverClean® photocatalytic topcoat, which incorporates titanium dioxide to reduce nitrogen oxide and sulfur oxide pollution while keeping the surface clean and bright.
Saint-Gobain has introduced Sheerfill Illuminate, a range of watertight membranes for roofing and façade applications where high light transmission is desired. Using the same proven materials long incorporated into Sheerfill — fiberglass reinforcement encapsulated with polytetrafluoroethylene — Illuminate products provide a high-strength-to-weight ratio, can be used as single layer tensile membranes, and provide the same peace of mind when it comes to safety with a Class A fire rating.
The Illuminate membrane will open a world of possibilities for architects and designers. The product can be varied to create options not seen before in the structural membrane market such as colored fabric with clear light transmission, different light transmission options — all with the design freedom possible only with reinforced membranes.
Saint-Gobain is working with several companies to realize some near-term projects, with plans to have a full launch during the second half of 2017. “Sheerfill Illuminate allows for increased light transmission to improve the comfort and sustainability of new structures of all types,” said Michael Lussier, global market leader, Saint-Gobain.
Automotive Composites
Composites are arguably the fastest growing segment of the textile market by percentage in emerging specialty applications, which include carbon fiber to reduce weight in the Boeing 787 aircraft, to various sporting goods from hockey sticks to golf equipment and even bicycles and wheelchair frames using resin, along with molded boat hulls. This market has the potential to explode if two things happen. First, if the Trump administration does not reduce current regulations that require automotive companies selling cars in the United States to average a minimum of 54.5 miles per gallon in 2025. This protocol termed lightweighting includes material offered by steel and aluminum producers and others who are diligently developing stronger lighter-weight metals as well as others who are introducing reinforced resins and plastics, some of which are already in production.
A second caveat is that carbon fiber, a rather modest sized market, is able to price its products in the $5- to $6-per-pound range — or perhaps even lower, depending on future lower-cost developments of alternative or in-kind materials. Watch these developments closely, as the final outcome could dramatically move companies and technologies. Man-made, inorganic bast fiber-textiles, including nonwoven fabrics are all widely used in composites for many other applications at hundreds of suppliers worldwide. Even if carbon fiber cannot match the price of other materials used in mass applications in automotive, other market segments are sure to grow at rates beyond gross domestic products over the next 15 to 20 years and perhaps longer, while providing handsome returns to many suppliers.
“While the composites industry has always been inextricably linked to lightweight parts, this year’s show was keen to highlight that high-volume composite parts aren’t a pipe dream, but a production-ready reality,” said Justin Cunningham, editor, Engineering Materials, reporting from the 2016 JEC show in Paris. “The question remains whether the technology is affordable and how long it will take to tool part suppliers for automotive.”
High-Performance Textile Finishes And Coatings
Whitford Corp., Elverson, Pa., is best known as one of the largest global suppliers of engineered coatings including sol-gel based coatings that provide lubrication and release for cookware and bakeware, as well as coatings for many industrial markets. Less well known to the textile industry is Whitford’s success in providing polymeric finishes and coatings to improve the performance and extend the life of fibers, yarns and technical textiles. “These emerging technologies are making a big difference in the properties and longevity of specialty use and technical textiles” said Spencer Siegel, global textile business manager.
Whitford’s custom technical textile finishes and technologies are used to improve the performance and greatly extend the life of automotive timing and conveyor belts, cargo nets, commercial marine and other high-performance rope applications. The company now offers BlisterGuard®, a range of low-friction yarns for athletic and military socks to reduce blisters, chafing and hot spots, while enhancing overall the wearer’s comfort.
Bio-Polymers Continue To Grow
Ingeo® polylactic acid sustainable polymers produced by Minnetonka, Minn.-based NatureWorks LLC are used to manufacture fibers for a wide variety of textile and nonwoven applications. As customers increasingly seek sustainable products, a large and growing number of global fiber, yarn and nonwoven fabric producers now offer materials for many end-use applications from filtration media to medical fabrics and apparel, as well as a broad range of packaging applications. NatureWorks offers a portfolio of Ingeo polymers that enhances the performance and sustainability of a broad range of fibers and fabrics. Companies are finding many of the unique and inherent properties such as wicking, breathability, skin comfort and ease of processing are valuable attributes for more sustainable offerings with improved performance. “The portfolio of fiber grade resins in the NatureWorks 6 Series are designed for processes from mono to multifilament as well as spunbond and meltblown products,” said Robert Green, global business director, Fibers/Nonwovens, NatureWorks.
Antimicrobial Medical Garments
Many antimicrobial textile technologies claim to reduce bacterial contamination on fabrics and use laboratory test results to infer effectiveness during actual use. Companies and brands can have their carefully built reputations ruined overnight and customers can be put in danger when products do not perform in real life.
To assist hospitals in their evaluation and decision making, American Hospital Association (AHA) Solutions Inc. conducted a thorough, proprietary due-diligence process review of antimicrobial solutions for the healthcare apparel market. AHA Solutions used evidence-based research to evaluate and document the effectiveness and safety of the products studied, and awarded its exclusive endorsement to VESTEX® Active Barrier Apparel produced by Orlando, Fla.-based Vestagen Technical Textiles Inc. The endorsements typically last for one to three years, and assist hospitals in making well-informed decisions about the most effective products to use.
Vestex differs from other antimicrobial apparel technologies. By incorporating a dual mechanism of action with fluid resistance in addition to an active antimicrobial with a rapid onset of action and a proprietary method of application, Vestex achieves enhanced effectiveness and comfort, according to the company.
The research efficacy of Vestex is reinforced by successful adoption and implementation by major health systems such as Northwell, Baptist, HCA Florida and overwhelming hospital staff satisfaction. “Based on effectiveness and safety, the American Hospital Association selected Vestex as the first and only apparel they have ever endorsed,” noted Ben Favret, president, Vestagen.
Editor’s Note: The author can be reached at Ed Gregor, Edward C. Gregor & Associates, LLC 803-431-7427 or by email ecg@egregor.com.
July/August/September 2017