REMSCHEID, Germany / SHANGHAI, China — October 19, 2023 — This year’s ITMA Asia + CITME 2022 trade show appearance of the Oerlikon Group will focus on current challenges that the entire textile industry has to deal with: creating a circular economy within the textile value chain, providing energy-efficient technologies, using digital solutions to support a sustainable production, processing new materials, and finally the traceability of all products and the recycling of raw materials used. And there are certainly many more subject areas that the visitors of the ITMA Asia -CITME 2022 will have questions about. Oerlikon therefore invites all trade fair visitors to engage in a dialog with all its experts at its booth in hall 7, A55. On more than 225 m², Oerlikon will give answers to the urgent questions of the present and the future.
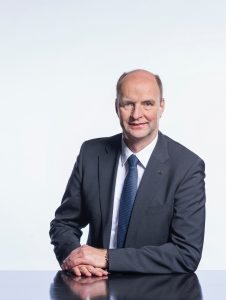
“At Oerlikon, we contribute with our innovative technologies for resource-saving use in almost all manmade fiber spinning mills in the world. Our promise for the future is to continue to expand the zero-waste production approach and thus take care of achieving our customers’ and our own sustainability goals”, says Georg Stausberg, CEO of the Polymer Processing Solutions Division and Chief Sustainability Officer of the Oerlikon Group. This sets out the claim of one of the world’s leading suppliers of machinery and plant solutions for manmade fiber production not only for this show: In the future, it will be solely a matter of sustainable innovations.
Circular Economy and recycling? Enabling customers to achieve more with less
Textiles are becoming an increasingly big polluter. To tackle the growing mountains of used clothing, it is above all European politicians who are developing a comprehensive strategy for a regulating circular economy. And the textiles industry is also making its mark with innovative technologies for recycling manmade fibers. However, there is still a long way to go before we have a sustainable textile world.
According to the European Environment Agency, the consumption of textiles is already the fourth-largest source of negative environmental and climate change impacts within the European Union (EU). A major reason for this is relentless textile growth: the Ellen MacArthur Foundation states that the global production of textile almost doubled between 2000 and 2015. And the annual consumption of apparel and shoes is expected to further rise by 63 percent by 2030 – from currently 62 million to 102 million tons – adds the European Environment Agency.
With this market development in mind, Oerlikon is intensively involved in Worn Again Technologies. The British partnership is focusing on a solvent-based recycling technology, with which both end-of-life textiles comprising polyester and polycotton blends and PET plastics can be converted into circular raw materials and fibers (polyester and cellulose). For this, a large demonstration system for upcycling 1,000 tons of textiles per annum is being created in Switzerland. “We are supporting technological innovators such as Worn Again Technologies because we believe their solution is extremely promising and because they are driving cooperation between the individual producers within the value chain. Recycling only works when all players cooperate in a circular system”, emphasizes Stausberg. He is already looking to the future: “The time for closed-loop strategies and the corresponding sustainable technologies is now – let’s talk about it at ITMA Asia + CITME 2022.”
In terms of sustainability, however, Oerlikon also sets itself high goals. Stausberg: “It is no surprise that we have applied high standards of innovation to our own operations and practices. For several years, Oerlikon has been creating pilot initiatives that we intend to implement company-wide to the greatest extent possible. For example, we are committed to achieving CO2 neutrality in all our locations by 2030 as we have already done at our site in Liechtenstein that provides our blueprint for meeting this commitment. Our goals also include obtaining 100% of our electrical energy from renewable sources and achieving the standard of ,Zero Harm to People’”.
In addition to regulatory initiatives, technical innovation is required to connect the beginning and the end of the linear textiles industry and to close the loop. One decisive circular technology here is fiber-to-fiber recycling. Only a few years ago, this process was used to recycle around just one percent of used clothing worldwide into fibers for new apparel. McKinsey market researchers are now talking about 18 to 26 percent being recycled by 2030 – if the full technical recycling potential is utilized and more textiles are collected. For this, manual processes will have to be automated, clothing waste qualitatively sorted, buttons and zips removed, and fiber compositions unambiguously identified – and all less expensively. Separating mixed fibers still represents an obstacle as well. Finally, the recycled materials must be suitable for the spinning process, provide a usable yarn quality and be able to be further processed, i.e., dyed. Despite these challenges, there are promising solutions on the horizon, even though some processes are not yet ready for commercial exploitation.
Oerlikon Barmag is offering technological solutions for rPET that enable customers to save million tons of CO2 per year. In 2022, Oerlikon Barmag introduced, a homogenizer recycling line specifically for customers in China and Asia where bottle flakes and film waste can be agglomerated, extruded, homogenized and melted to produce polymer melt or chips. It enables the polymer quality of recycled bottles or film waste to be precisely adjusted to the requirements of different downstream extrusion or injection molding processes.
Another rPET solution is the VacuFil system from the Oerlikon Barmag joint venture, BB Engineering. VacuFil is a unique and innovative PET recycling line, uniting gentle large-scale filtration and targeted intrinsic viscoscity (IV) regulation for consistently outstanding rPET melt quality. In 2022, BB Engineering launched a patented key component of the VacuFil system, the Visco+ filter as a separate and easily integrable upgrade component that enables precise IV setting and pure melt with the help of vacuum. IV is the central quality characteristic in PET recycling and rPET processing. It determines the melting performance in the production process and the properties of the end products and is thus essential in the recycling process. The Visco+ process is reliable, verifiable and 50% faster than conventional liquid-state polycondensation systems.
Energy Efficiency? EvoSteam process revolutionizes polyester staple fiber production
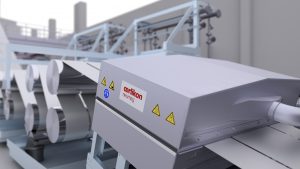
There is a huge demand for textile fibers: population growth of around 3% per annum, fast fashion and many other factors are fueling this demand. According to international studies, global demand for staple fibers made from polyester will total 20 million tons in 2025 – this is approx. 33% more than the production volume recorded in 2013. In view of noticeable climate change and its impact on people and the economy, resource- and environment-friendly manufacturing methods are absolutely crucial for the future. High production costs are currently eating into the margins of fiber producers. Noteworthy here are above all massively increased energy and polymer prices, but water is also an important resource today – very frequently scarce and consequently expensive. At this year’s ITMA Asia + CITME 2022 in Shanghai, Oerlikon Neumag will be unveiling its new EvoSteam process to interested trade visitors, viewed by many process experts as an enabler for more sustainable staple fiber production in the future. The objective of the new development is to lower both operating expenses (OPEX) and the carbon footprint with minimal consumption of energy, water and polymer – simultaneously with the excellent fiber qualities demanded by downstream processes and high production volumes.
New Materials?
Looking back at the regulations of the European Union, among others, there are also major challenges for new materials. In that regard the Green Deal can only be realized if new European Union policy frameworks create certainty for future investments.
“In the polymer processing industry, we have to come to a sustainable, closed circular economy for packaging materials and textiles, for example, while simultaneously intensively expanding the recycling of the materials used. Here, new materials also offer opportunities – opportunities that we as a machine manufacturer and plant engineering company will exploit. However, compared to non-biodegradable, petrochemical-based polymers such as PE, PET and PP, the prices for bio-based polymers like PA 5.6. and biodegradable polymers like PLA, PBAT and PBS are not yet competitive. In contrast, the properties of bio-based materials used for consumer products, especially those used in the packaging industry, are already competitive. It appears compostable textiles will remain a niche market”, explains Stausberg.
“But one thing is certain: utilizing current Oerlikon technologies and future innovations, we will be able to transform virtually any raw material into an ecologically attractive end product. The economic questions will ultimately be answered by consumers. Technology is once again enabling us to create a better world”, says Stausberg.
Digitalization and Traceability?
With its sustainable and closed loop-compatible textiles strategy, the EU plans to become a pioneer for the global circular economy as well. By 2030, textile products marketed within the EU are to become more durable and recyclable, predominantly comprise recycled fibers, contain no hazardous substances and be manufactured in compliance with social rights and in a manner that protects the environmental. This also includes the introduction of a digital product passport and the amendment of the European Textile Labeling Act: To implement the closed-loop principle and other important environmental requirements, players along the value chain must also fulfill new information obligations about the composition of textiles. At the show, Oerlikon will present own digital technology solutions and those that have been tested in collaboration with various partners for the use in Oerlikon technologies.
Looking into the future with the Oerlikon Barmag Digital Twin
The term “digital twin” was coined in 2014 by Michael Grieves and John Vickers (NASA) and is used and interpreted for different scenarios: The simplest digital twins map a digital inventory list of a real machine, for example, in order to be able to supply exactly matching spare parts for a customer-specific plant. At the other end of the complexity scale are digital twins that map the kinematics and/or dynamics of a machine or plant. At ITMA Asia + CITME 2022, Oerlikon Barmag will present a complete WINGS POY winding head as a kinematic model as a digital twin. For this purpose, all essential machine components were modeled as rigid bodies and connected to each other via joints and contact bodies. The actuators present in the real world were simulated by forces and moments. Analogously, the sensors are simulated by contact bodies and corresponding collision bodies. With this kinematic model, it is now possible to map all the processes that occur during the operation of a winding head in virtual space. Customers can thus be offered faster and more cost-effective production solutions.
Digital Academy – its just the beginning
Interactive and customized, modular and flexible in terms of time – all features of a modern training concept. Adapted to the needs and general conditions of the respective student, training sessions should be independent of time and place and the contents should be tailored. This concept is being implemented within the Digital Academy at Oerlikon. The digital online training center, available through the myOerlikon.com e-commerce platform, comprises a collection of role-based e-learning modules on such topics as operation, maintenance and repairs – currently for the Oerlikon Neumag BCF S+ and S8 machines. Training is targeted at operating staff, process engineers and technicians, and quality assurance officers. The Digital Academy learning contents are available for the Oerlikon Neumag BCF S+ and BCF S8 systems. Further contents will be continually expanded and made available to all customers.
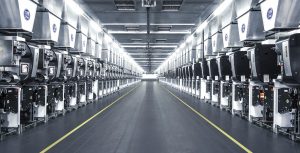
Oerlikon Barmag ACW WINGS
How can an upgrade increase Oerlikon Barmag POY yarn manufacturing process quality while simultaneously cutting energy consumption, waste, time and personnel? At ITMA Asia + CITME 2022, Oerlikon will show its long-awaited upgrade: ACW WINGS drawing fields. Established technologies can always be made better. When the Advanced Craft Winder (ACW) was launched in 1998, it was truly convincing with its sophisticated modifications for initial string-up and yarn transfer. WINGS replaced it as the new benchmark in 2007. However, because Oerlikon Barmag technology last for decades, many ACW and WINGS winders are being operated practically side-by-side in some places. Customers asked Oerlikon: please build a WINGS drawing fields over our ACW winders! At ITMA Asia + CITME 2022 it will be shown in hybrid way – a WINGS drawing field in combination with virtual ACW Winder.
Oerlikon Barmag Wiping Robot
Regular wiping of the spin packs is important for process stability and yarn quality. Automating the process with Oerlikon Barmag’s wiping robots, which can be retrofitted to numerous spinning plants, delivers considerable benefits, as it reduces the yarn break rate by up to 30%, improves process stability and reduces downtime. In addition, wiping robots help to indirectly reduce waste as a result of a 90% decrease in the use of silicone oil spray cans and a 15% to 20% decrease in total silicone oil consumption.
Oerlikon Nonwoven HycuTEC
Oerlikon Nonwoven’s HycuTEC inline charging technology is used to create high-end charged meltblown filtration media. Introduced in March, it went on to win the 2022 FILTREX™ Innovation Award. One of the reasons HycuTEC won the award was that the meltblown media treated with the technology requires 40% less polymer (fabric weight) to achieve the same filter efficiency than the nonwoven material that was not treated. In other words, filter specification is easier to achieve while reducing waste in production. Compared with other hydro-charging concepts, the unit significantly reduces water and energy consumption due to the elimination of an additional drying process and the lower pressure drop in the filter material. HycuTEC is the first industrially manufactured hydro-charging solution that can be easily retrofitted to existing systems as a plug-and-produce component.
Posted: October 19, 2023
Source: Oerlikon Group