OBERTSHAUSEN, Germany — More benfits and maximum delivery reliability – these are the benefits that KARL MAYER is offering customers of its Raschel machines for special applications with a new fabric batching device.
The batching device bears the designation 26 B and is once again manufactured in-house for added value. In-house production guarantees punctual production in accordance with the production plan for the overall machine. In addition, the use of proven standard parts made by KARL MAYER and the innovative company’s design expertise ensure durability and continuous optimization.
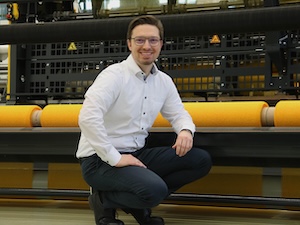
“We are now more resilient in our dealings with suppliers and can drive forward further developments to our batching device more efficiently,” explains Sascha Cron, Head of Customized Raschel Machinery Development at KARL MAYER’s Warp Knitting Business Unit.
More convenient operation, safer working
The first generation of the 26 B batching device already demonstrates what is possible in terms of upgrades.
The new solution offers particular advantages in terms of handling over the previous version. By integrating its control system into KAMCOS® 2, the required settings can be conveniently entered and read on the machine’s operator interface instead of on an external display. Nothing changes for the user in terms of content. All familiar functions remain available. The uniform control via KAMCOS® 2 without system breaks also minimizes the susceptibility to errors and enables regular, simple updates of the drive controller remotely and according to standard routines.
A further advantage for the personnel is increased work safety. If the batching device is used with a needle coating, a system consisting of three light barriers and a protective grill across the entire width of the batching device prevents access with the risk of injury during machine operation. Batching devices with a conventional coating are secured with four light barriers.
A drive concept with less complexity while maintaining the same rotational movement and therefore unchanged fabric flow round off the current extensive benefits package of the 26 B batching device.
Room for further innovations
Further functional features can be implemented promptly on request. For example, an ejection device for heavy fabrics can be integrated into the batching device 26 B if required, thus reducing the manual effort. A traversing device is also possible to ensure an even selvedge build-up. The targeted displacement movement prevents the pillar stitch from piling up at the edges, which can cause slipping. Another potential option is to equip the batching device with a pressure roller. After changing a fabric beam, the additional component ensures reliable contact between the roller and the still-empty cardboard tube, and therefore a slip-free transfer of the rotational force. This allows perfect fabric tension to be achieved right from the start.
Available as standard and retrofit solution
Following comprehensive and successful functional tests, the 26 B batching device was released for sale in January of this year and had already been ordered by four customers by mid-February. The component is available as a feature of the standard specification of new machines. KARL MAYER’s spare parts range also includes retrofit solutions for existing machines, both with KAMCOS® 2 and KAMCOS® 1. The retrofit version for KAMCOS® 1 machines also includes a modern external display with touch function. This means that users of older machines can also benefit from the excellent quality and functionality of the new 26 B batching device to ensure their continued successful production.
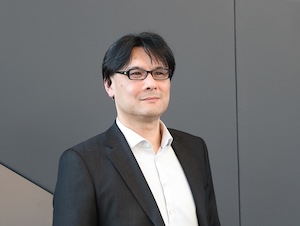
Tetsuji Yasumura from the KARL MAYER Care Solutions team is pleased to receive inquiries about replacing existing batching devices with the new 26 B variant on Raschel machines in practice.
Posted: February 20, 2025
Source: KARL MAYER Verwaltungsgesellschaft AG