OBERTSHAUSEN, Germany — May 23, 2024 — The control and reduction of energy consumption and in turn, of costs and CO2 emissions – no more and no less. This is what the KARL MAYER GROUP offers its customers with its new Energy Efficiency Solution. The innovation, which runs via the technology platform of KM.ON, helps warp knitting companies achieve less electricity waste and more sustainability, and shows the potential that arises from close cooperation among mechanical engineering, service and digitalization specialists.
Markus Bahde (MB), Product Owner Digital at the KARL MAYER GROUP, talks with Ulrike Schlenker (US) from Corporate Communication at the KARL MAYER GROUP.
US: How did you come up with the idea of developing the Energy Efficiency Solution? What encouraged you to take this step?
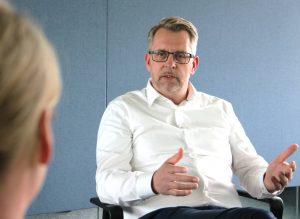
MB: When designing and developing new solutions, we rely on our longstanding expertise in research and development and incorporate the innovations in our digitalisation. In general, we work closely with our sales team: we have our ear to the ground and hear what our customers are saying. Like all production companies, warp knitting companies are currently under severe pressure in terms of energy costs, sustainability and documentation requirements. But there are also numerous national support programmes that support measures for reducing the energy consumption of production units, including ones for industry. At the beginning of March, Italy adopted a decree-law to introduce the Transition 5.0 plan, thereby deciding to invest €6.3 billion in digitalization and the energy transition. Obviously, our development focus is the right one. This was already evident at ITMA 2023. At the leading textile machinery trade fair in Milan, we previewed our prototype to the specialist public and received very encouraging feedback. Many guests expressed their interest.
US: Why was the response so positive? Please explain what the new digital development offers customers and the benefits they can derive from it in more detail.
MB: The Energy Efficiency Solution offers multi-faceted support for warp knitting companies in energy management, including the display of real-time energy data for individual machines and the entire machine fleet, the analysis of historical energy data and the creation of energy reports. When the machine is heating up, it also enables efficient control without on-site manual adjustments. With these features, customers can take effective action to reduce energy consumption, electricity costs and CO2 emissions. A test customer was able to achieve a monthly energy saving of approximately 5% to 10% within a short time.
US: That is a significant amount! Are further steps planned or do you already have further developments in mind?
MB: Yes, we have already identified other use cases and prepared them on the system side. They will enable our customers to carry out additional and more detailed analyses. In addition, we constantly evaluate market feedback to continuously optimise and expand our solution to enhance customer value. The results will be incorporated into further release updates later this year. We are also planning major updates, which, alongside monitoring, will also optimise energy consumption. As a first step, in future, the Energy Efficiency Solution will independently make recommendations for action to reduce energy costs and CO2 consumption. In addition, we are planning to continuously expand and improve our services around machine condition.
US: Where and when can customers experience the performance of the Energy Efficiency Solution for themselves?
MB: The solution for more energy efficiency will be a highlight of our exhibition at ITM. The mechanical engineering fair will take place from 4 to 8 June in Istanbul. We are also planning a presentation at the ITMA ASIA + CITME from 14 to 18 October in Shanghai. We are looking forward to welcoming many visitors. Of course, interested persons can also contact us directly. We can be reached at caresolutions4u_wk@karlmayer.com.
Posted: May 23, 2024
Source: KARL MAYER GROUP